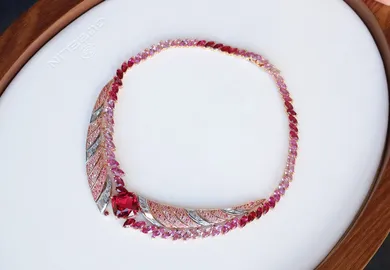

Superior Spinels: How Minehaus Brings Artistry to Gemstone Cutting
On a recent visit to Jaipur, India, I had the pleasure of spending a day at Minehaus – a local gem-cutting company founded in 1981. What was initially launched by Subhash Chhabra as a small business has now evolved into gemstone faceting and selling offices at Johari Bazar (Jewellers’ Market) located in the heart of the Pink City. It remains a family business and is currently run by Subhash’s children – Harsh and Shubham Chhabra. Today, Minehaus is known for producing top quality gemstones, and not just the traditional shapes, but fancy-cut and portrait-cut spinels, garnets, corundums and beryls, exquisite ruby beads, cabochons, and carvings. Let’s go behind the scenes of a business that’s daring to be different…
Personally, when I think of Minehaus, spinels in all sorts of shapes and sizes come to mind, maybe because this is what I see most of on their Instagram. ‘Spinels provide us with a variety of colours that can be used by designers for innovative creations. In the past, I feel that spinels were underrated, but now more people are getting to know them and “fall in love with,” according to Harsh Chhabra as we browse a wide variety of gems in his office.
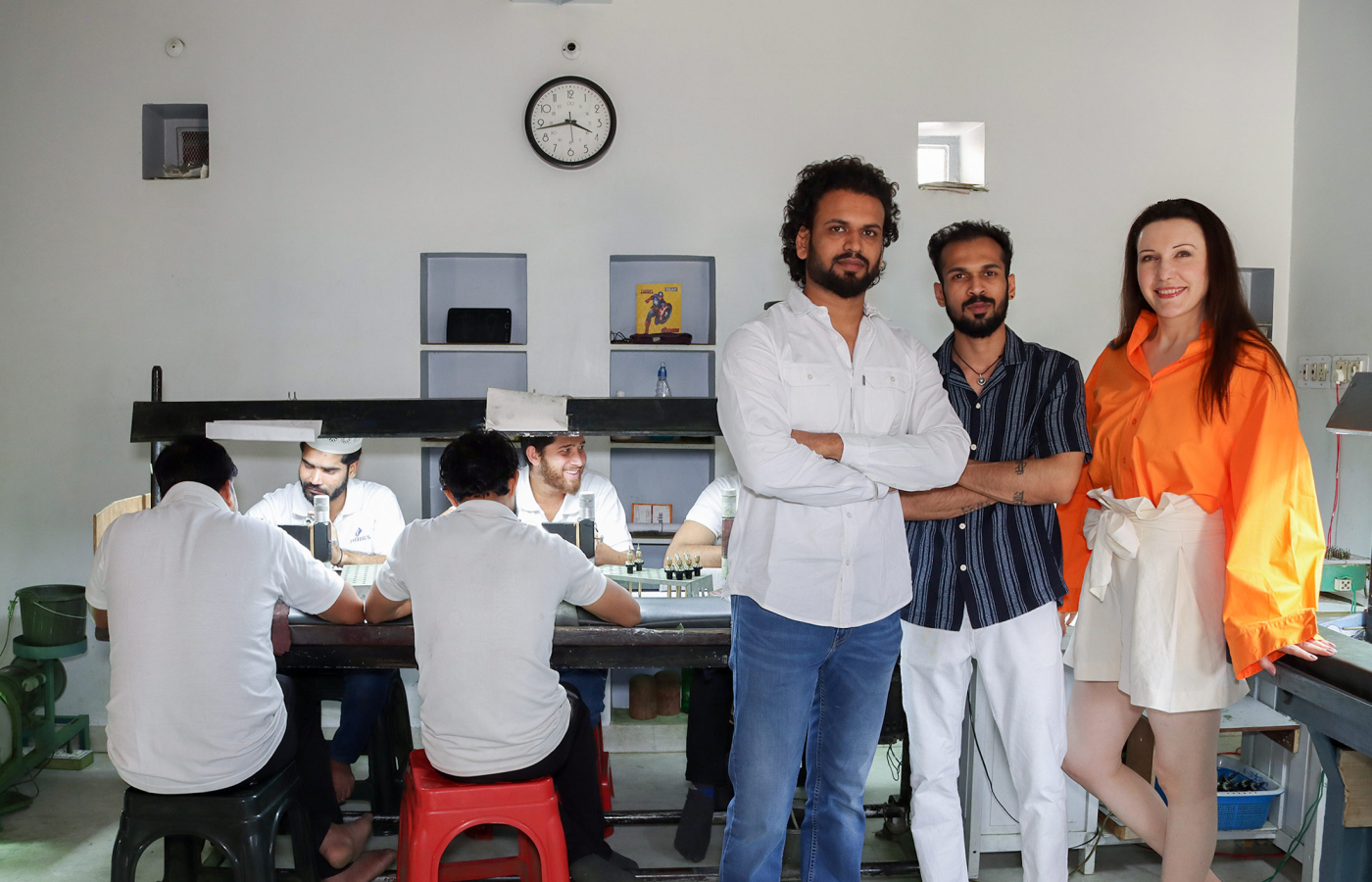
Katerina Perez with Minehaus directors Shubham (left) and Harsh Chhabra
In the 1980s, Minehaus was involved in the extraction of gemstones from mines around the world, specialising in ruby, emerald, sapphire, alexandrite, aquamarine and lesser-known gems like cat’s eye chrysoberyl, rhodolite and iolite. By the 1990s, it was known as a consistent supplier of raw materials with an expanded remit including spinel, tanzanite, mandarin garnet and tourmaline.
Minehaus started manufacturing rubies in the year 2000 with its unique techniques of cutting and polishing. But something changed when the new generation joined the business and took it to the next level by manufacturing other exotic stones like spinel, mandarin garnet, sapphire and tourmalines. Harsh and Shubham Chhabra were the energetic next generation in the Minehaus family, and both wanted to expand the business’ boundaries. They took a revolutionary step forward and created a production house to transform rough material into unique and fancy-cut gemstones. What first drew my attention, however, was the flair that Minehaus brings to its own craft. This isn’t just gemstone cutting… it’s a chance to be artistic and adventurous.
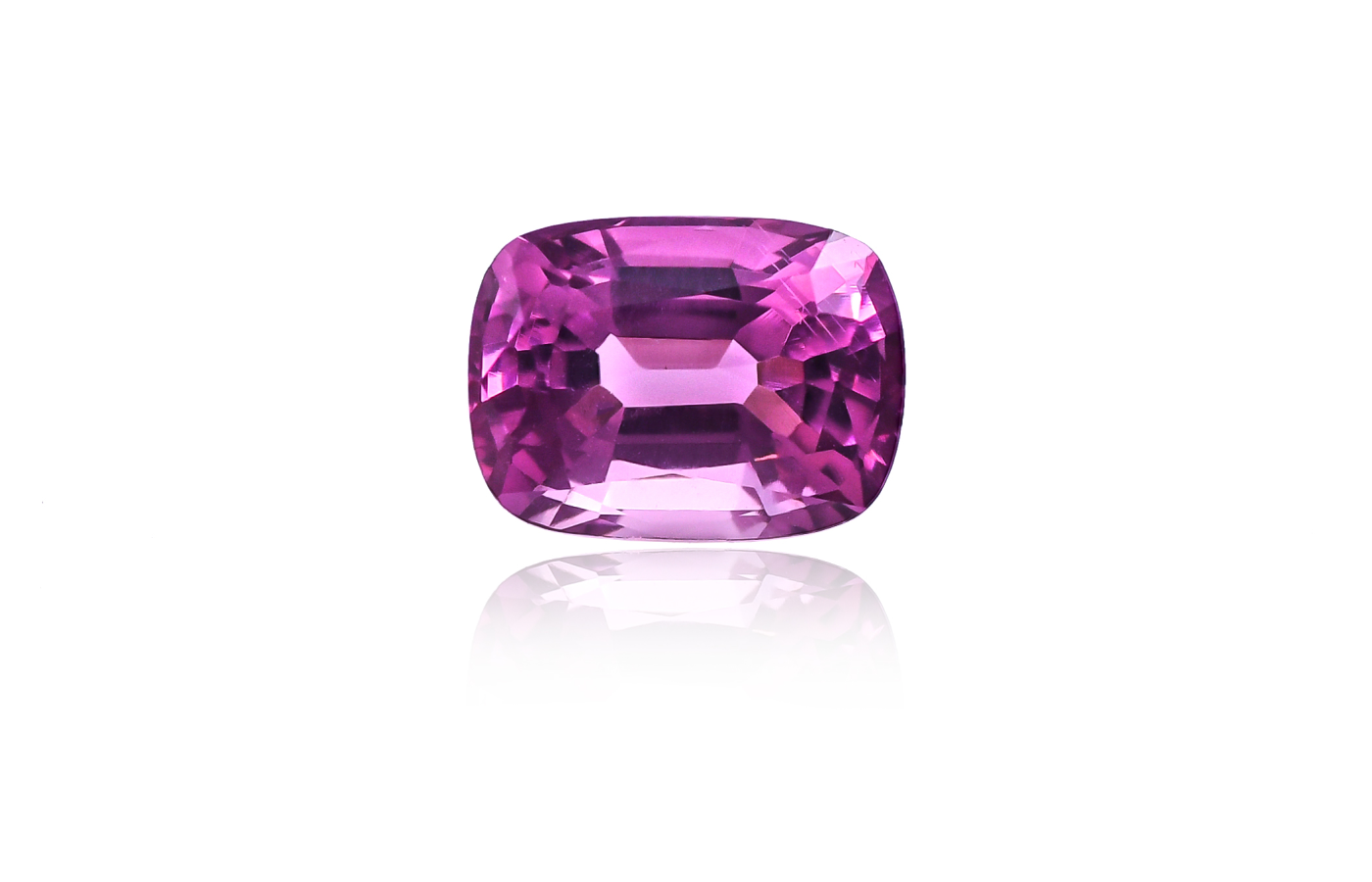
Minehaus mauve spinel of approximately 5-carats
We take pride in offering a curated selection of rare and distinctive gemstones, ensuring our customers access an exclusive range that goes beyond conventional cuts and varieties that many other companies offer. – Harsh Chhabra
When I visited the home of Minehaus in Jaipur, my focus was firmly on hot pink-to-red, blue and purple spinels and the process of transforming a rough mineral into an expertly faceted gemstone. Its hardworking team of nine specialists can facet somewhere between 120 and 200 stones per day, with one person focusing on preforming the table, another on calibrating the stone, and someone else on polishing the girdle. It never ceases to amaze me that one person can dedicate their professional life to something as nuanced as a single facet, but it takes this level of laser focus to become a true specialist!
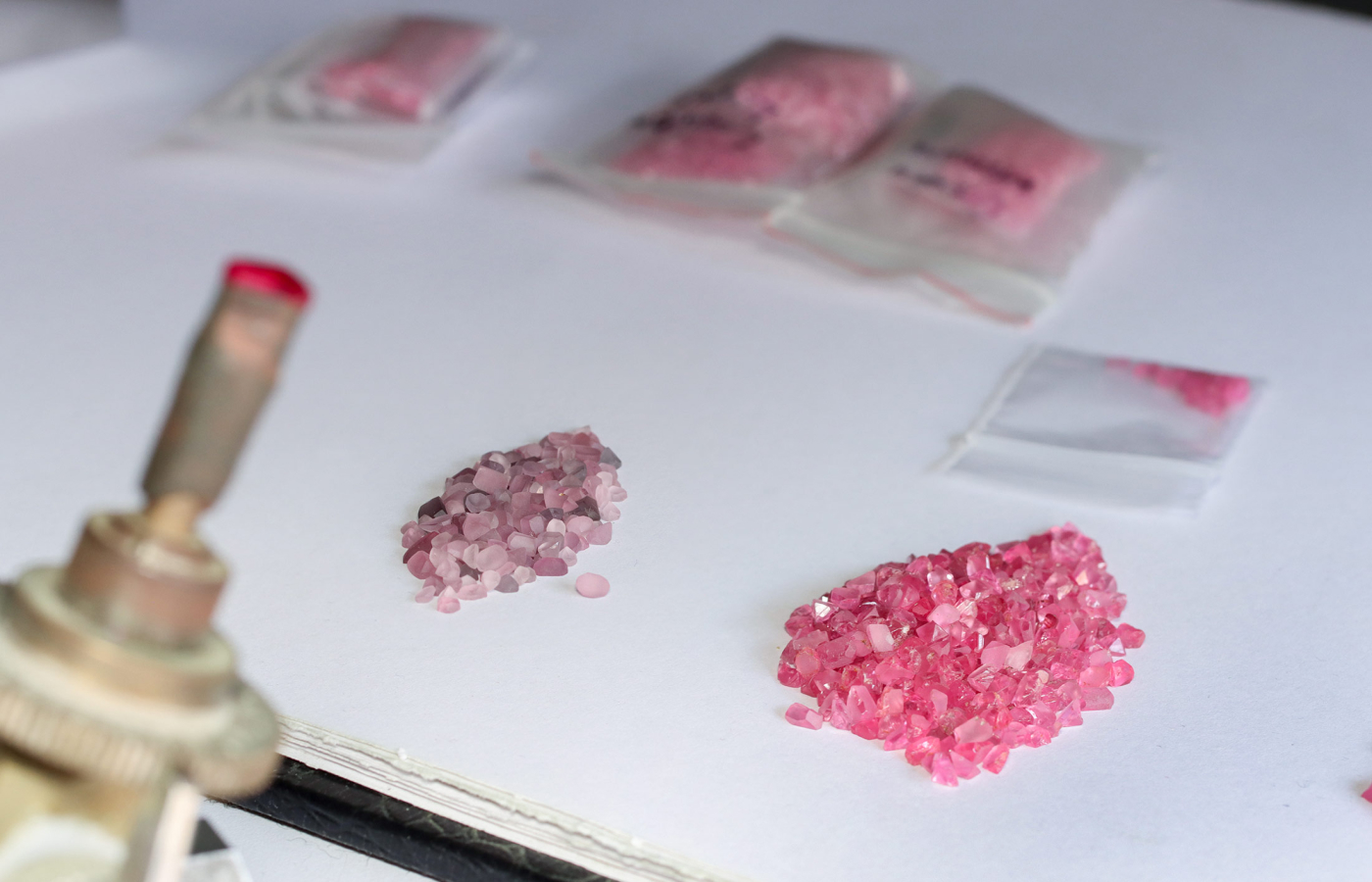
Preformed spinels at Minehaus' facility in Jaipur, India
Before I share some behind-the-scenes insights from the Minehaus cutting process, let’s talk spinel. For centuries, this gemstone was confused with ruby and didn’t have its own identity. In Hindi they are called “Naram Manak” which translates as ‘Soft Ruby’. Thankfully, times have changed, and spinel is a commonly featured gemstone in high jewellery collections, especially the intensely pink and red varieties from Vietnam. It also forms in shades of orange, purple, blue and black, so there’s plenty of opportunity for designers where this once-underappreciated gem is concerned. “We always loved working with rubies, and this has been one of our specialities since my father founded the company,” notes Shubham, “so that’s another reason for us to explore spinels.”
Purchasing The Rough Material
Step one in the spinel cutting process is preforming the rough. When Minehaus buys directly from mines, it secures large bundles of mixed rough material in large and small sizes of different quality mixed altogether. This variety in size and quality means rough has to be assessed and sorted in terms of its potential when it reaches the office. Some may be pristine enough to become a high-quality faceted gemstone, whereas others may be better suited to cabochon forms or even beads.
Assessing The Rough Material
Now, imagine you have a chunk of this material, almost straight from the ground, and you need to turn it into a cushion-cut gemstone. Where would you start? First, you’d look for fissures and inclusions – features that could make the stone vulnerable during the cutting process or impact a polished stone’s beauty. This typically requires creating a ‘window’ into the stone by sanding one surface, which allows the craftsman to see where might be most suitable for the table facet (the largest facet on the crown of a gemstone). As this is where the most light enters a stone, it should be free of inclusions like silk that create a hazy appearance. Minehaus may also decide to transform one larger piece of rough into multiple smaller gems.
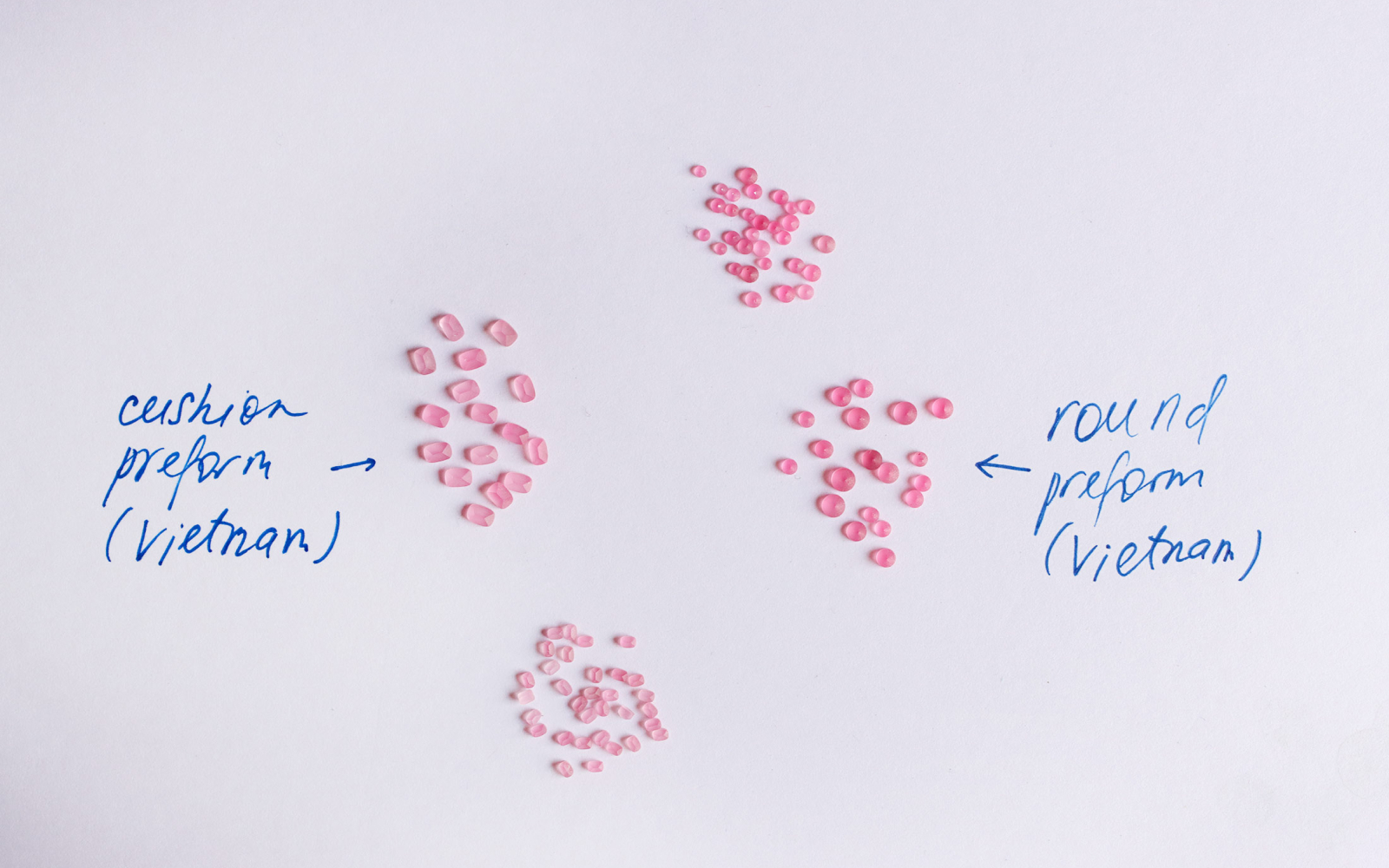
Minehaus highlights how preforming lays the foundations for the eventual cut and shape of a gemstone, such as the cushion and round Vietnamese spinels seen here
Preforming The Rough Material
Next, there’s preforming or the process of creating the inaugural shape of a gemstone using a high-density sanding disc. The main thrust of preforming is laying the foundations of the eventual cut with the all-important table facet, which should be clean and free of inclusions. During this process, much of the weight can be lost, but this ultimately leads to a superior finished product. Once the table facet is in place, the spinel will move onto another person…
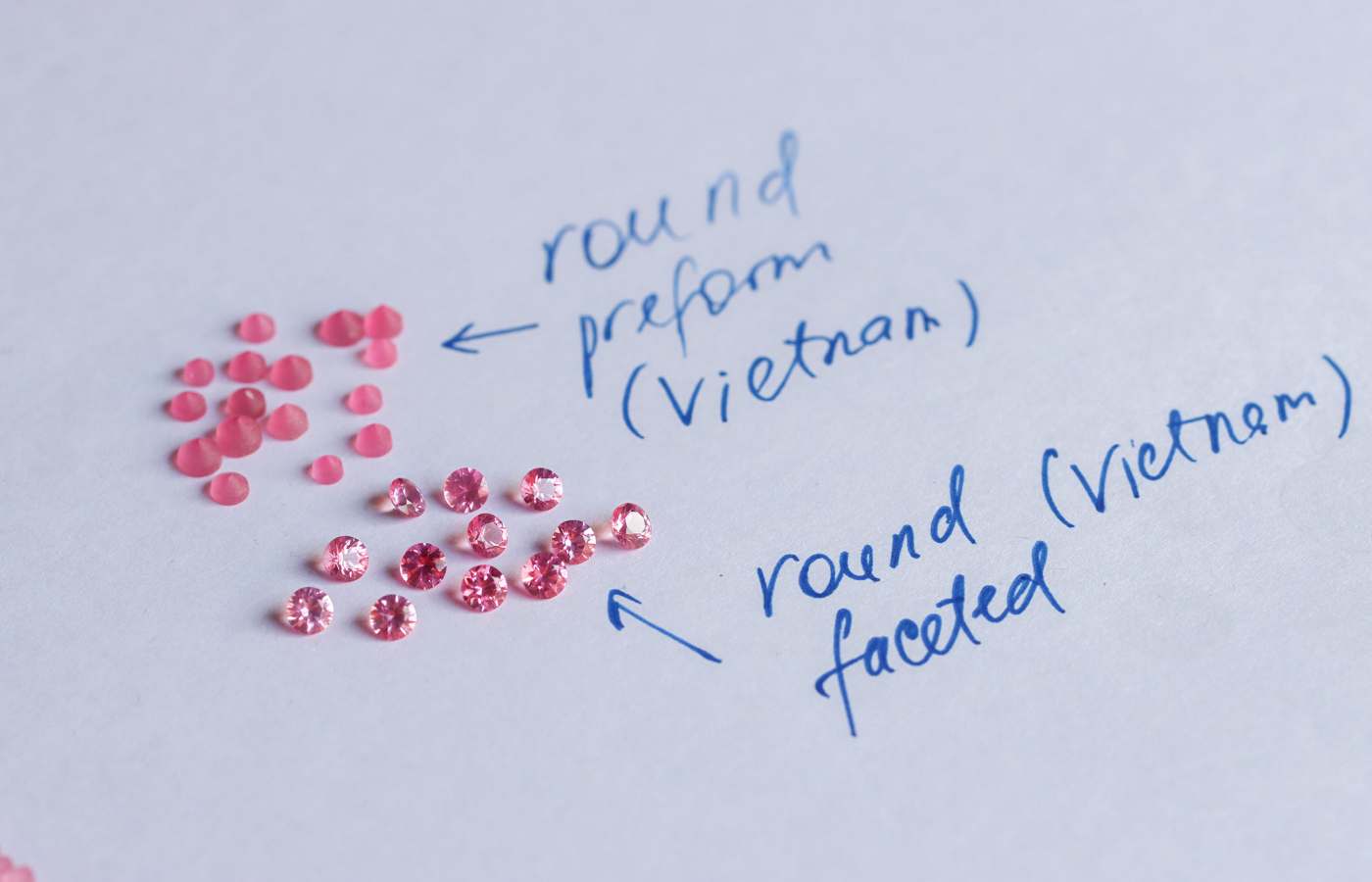
Minehaus presents preformed Vietnamese spinels and the finished faceted round gemstones, ready for jewellery
Calibration, Cut & Polish
We know that the ideal cut gemstone is all about proportions, so the next phase is calibration and cutting. The first step is ‘cropping’ a rough into suitable dimensions for its eventual cut, such as cushion or round brilliant. Using the table as a guide, another craftsman will ensure the height and width of a stone are proportional for maximum beauty and light return. One thing I discovered during my visit to Minehaus is that spinels with perfectly elongated octahedral shapes lend themselves beautifully to cushion cuts, as this allows for maximum weight to be preserved. “The best weight you could get out of square octahedrons would be round or square [gemstones], so we decide the shape according to this structure,” Shubham explains.
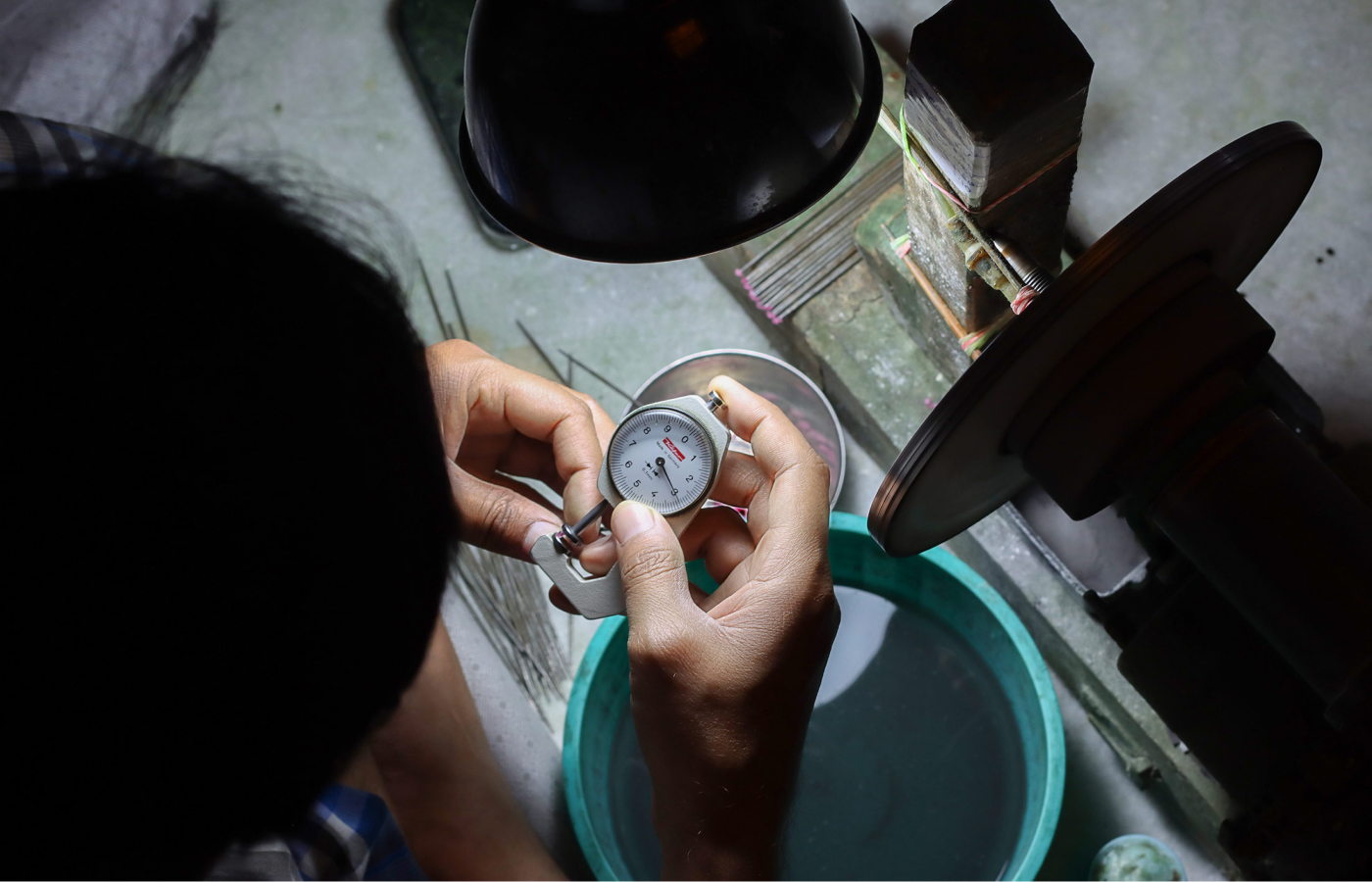
A Minehaus gem-cutting expert perfectly calibrates a stone to ensure it has the perfect proportions
Our company stays at the forefront of gemstone cutting technology, constantly innovating and employing cutting-edge techniques to create distinct and exceptional gemstone designs. One of the techniques invented by us is polishing ruby beads on diamond-coated pure sandalwood to enhance their shine. – Shubham Chhabra
Cutting and polishing a spinel is all about discs. Think of these as polishing wheels made from different materials and embedded with higher or lesser densities of diamond powder to grind and shape a stone. Harsh tells me: “As you continue through the stages of polishing, each one becomes more intense, and the surface level becomes flatter and flatter. The higher the microns [of diamond powder], the better the polish will be.” I was also surprised to discover that one disc is made of goat hair, as this is specifically used to polish the girdle of a gemstone (the widest point where the bottom of the crown meets the top of the pavilion). It’s a soft material, so it won’t chip the girdle, risk trimming weight from the stone or altering its shape.
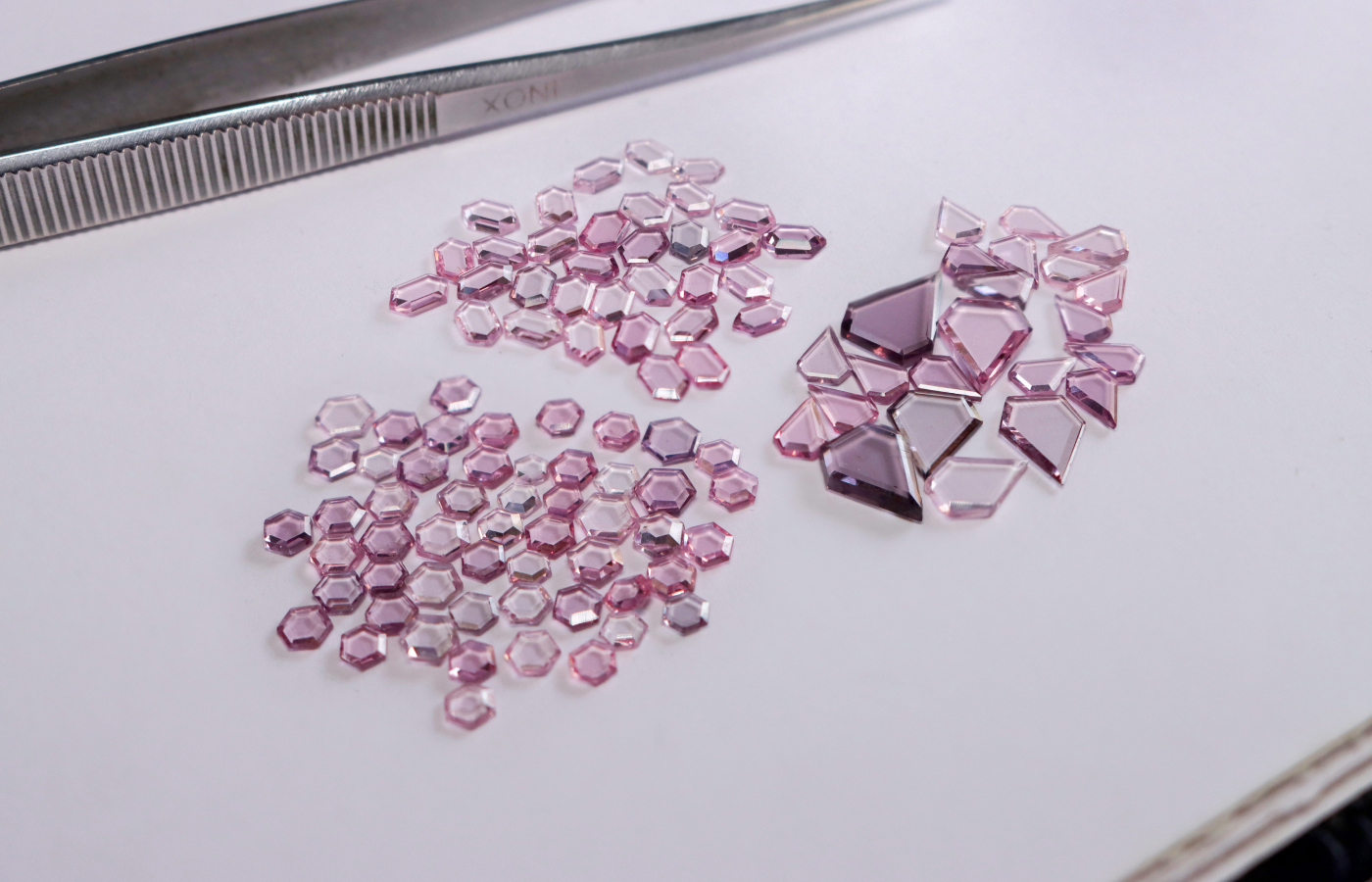
Minehaus portrait-cut spinels from Tajikistan and Vietnam
Sorting Gemstones
Although this process may sound complicated (which it is!), there is a dedicated sorter in the team who is so experienced that assessing a gemstone is his second nature. “We practice every day, we have mastered it,” Harsh tells me. “We need to darken the room and have only one source of light that reflects on the facets that you want to see. This way, the colours are true and can be separated. If there are too many light sources, the whole stone will basically be illuminated and we might omit the nuances of colours.”
Minehaus will sort its cut and polished spinels based on clarity and size, of course, but also the particular shade they exhibit, whether that’s electric pink, a deeper rose or red. It may also choose a specific selection of tonally similar spinels for interesting layouts to give its clients inspiration for future earrings and necklaces, which is something I love to see. Again, it’s another individual who specialises in the process of grouping gems into their respective categories, often spending hours in a darkened room to accurately assess each stone, one by one.
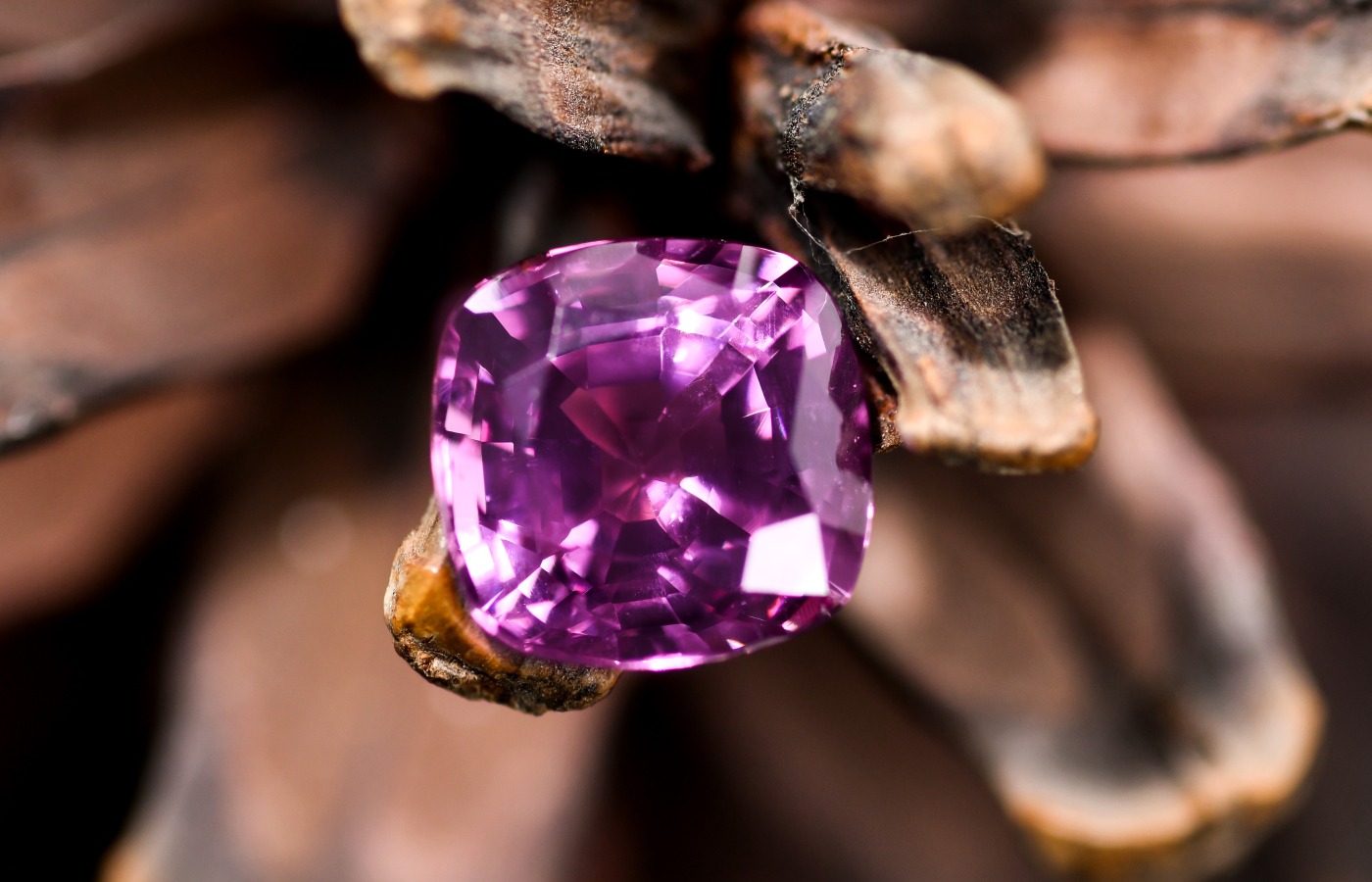
A sensational purplish-pink spinel of 6 carats from Tajikistan, crafted by Minehaus in Jaipur, India
A Different Approach
During my tour of the Minehaus facilities, a selection of cute and dainty cushion-cut spinels caught my eye. Each was beautifully cut but very small, likely suited to pavé or a high jewellery watch. Now, bear in mind that these tiny gems are difficult to produce and, ultimately, less in demand than larger carat weights… why does Minehaus go down this route? “It takes a lot of time to make these small stones, but we want to do something different. We’ll create the demand,” Harsh shares as a Creative visionary behind the company. “Our clients understand that it takes a lot of time to make these; it’s not so easy, which is why not everyone makes them.”
This trend-setting approach to gemstone production is what initially drew me to Minehaus, as well as its focus on ‘exotic’ gemstones and fancy cuts, of course. Harsh says: “Beyond the technical aspects, our gemstone cutting is infused with an artistic vision that elevates each piece, making it not just a gemstone but a work of art that tells a unique story.” Clients can tap into this vision by commissioning their own tailor-made gemstone cuts or by requesting one-of-a-kind gems that reflect their personal aesthetics.
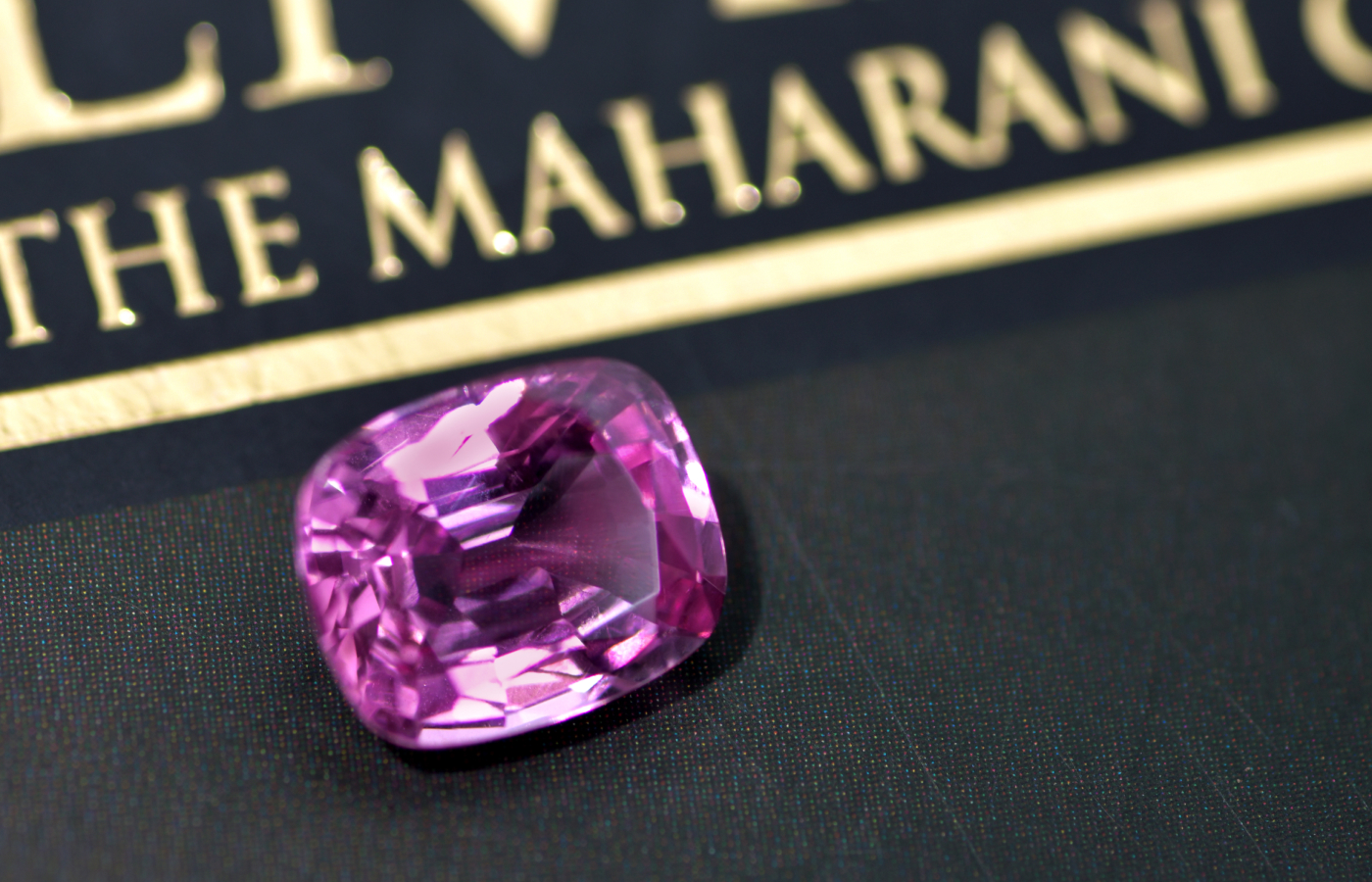
Minehaus presents its clients with exceptional gemstones, including this purplish-pink spinel from Tajikistan weighing more than 7 carats
I will let you in on a secret… I think I’ve already found my dream Minehaus gem! I called it the ‘Purple Passion’ – a 25-carat purple spinel from Tajikistan that I shared on Instagram. If you’re seeking a gemstone supplier that brings out your dreamy, romantic, artistic and daring side, I recommend adding Minehaus to your list.

WORDS
Katerina Perez is a jewellery insider, journalist and brand consultant with more than 15 years’ experience in the jewellery sector. Paris-based, Katerina has worked as a freelance journalist and content editor since 2011, writing articles for international publications. To share her jewellery knowledge and expertise, Katerina founded this website and launched her @katerina_perez Instagram in 2013.
Related Articles
Latest Stories
Add articles and images to your favourites. Just

Epic Evolution:Miseno Launches the Arco Collection to Celebrate a Fabulous Decade
I am pleased to present to you my highlights of the new Arco High Jewellery collection, which was formally showcased to the jewellery world at Couture from June 4-8, 2025
Jewels Katerina Perez Loves
Continue Reading

In Conversation:Discussing Paraiba - The Legacy of a Color
with Vogue Singapore
Brand Focus: Pomellato
Jewellery Insights straight to your inbox